In addition to workforce training and large scale information and training campaigns with the continuous support of the company’s top management, activities include: reviewing the qualification and feedback criteria on the companies that work for eni and the obligatory definition over the last nine years of managerial objectives related to the accident statistics for all sectors of the business.
These measures have produced a positive trend in the data on accidents and a continuous improvement in performance.
eni’s improving trend was confirmed by the Total Recordable Incident Frequency index for its workforce, which in 2012 was already the best in the industry.
The Lost Time Injury Frequency (LTIF) index showed a record value of 0.35 while the Total Recordable Incident Rate (TRIR) was 1.04.
eni has analysed the accidents and injuries that occurred in 2013 (213, 75% less than in 2006). The majority (6 out of 10) can be attributed to behavioural aspects such as lack of attention, following the procedures or poor working methods. Accordingly, after the analysis of root causes, action has and will be taken to reduce the most common causes of serious accidents, such as falling from heights, accidents while commuting to and from work, handling pipes and working in confined spaces.
The work to bring about cultural change will therefore continue, in particular for contractors and suppliers with direct communication initiatives extended to the workforce at the main operational sites, involving the whole eni team from the business lines to human resources, procurement, legal affairs and HSEQ. The key messages to be conveyed are the strong and continuous commitment of management, the importance of operational control and zero tolerance for those who do not respect the rules, the new qualification and feedback process for suppliers. eni will identify from within its operating sites safety leaders who will use their passion and courage to create a culture in which safety is the driving value.
Accidents and LTIF of eni’s workforce
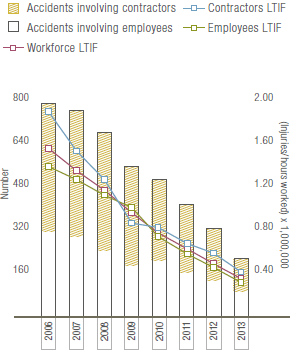
Total Recordable Incidents (TRIR)
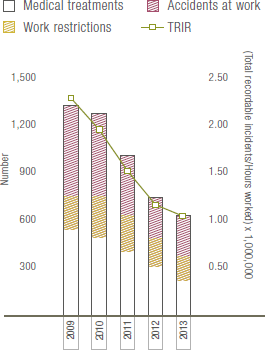